Najlepsze płytki do stali hartowanej w 2025 roku: Poradnik eksperta
Zastanawiasz się, jakie płytki do stali hartowanej wybrać? W obróbce twardych materiałów, takich jak stal hartowana, kluczowe są płytki z węglika spiekanego, a diamentowe (PCD) dla ekstremalnych wyzwań. Odpowiedni wybór to nie tylko kwestia efektywności, ale i przysłowiowego "świętego spokoju" na hali produkcyjnej.
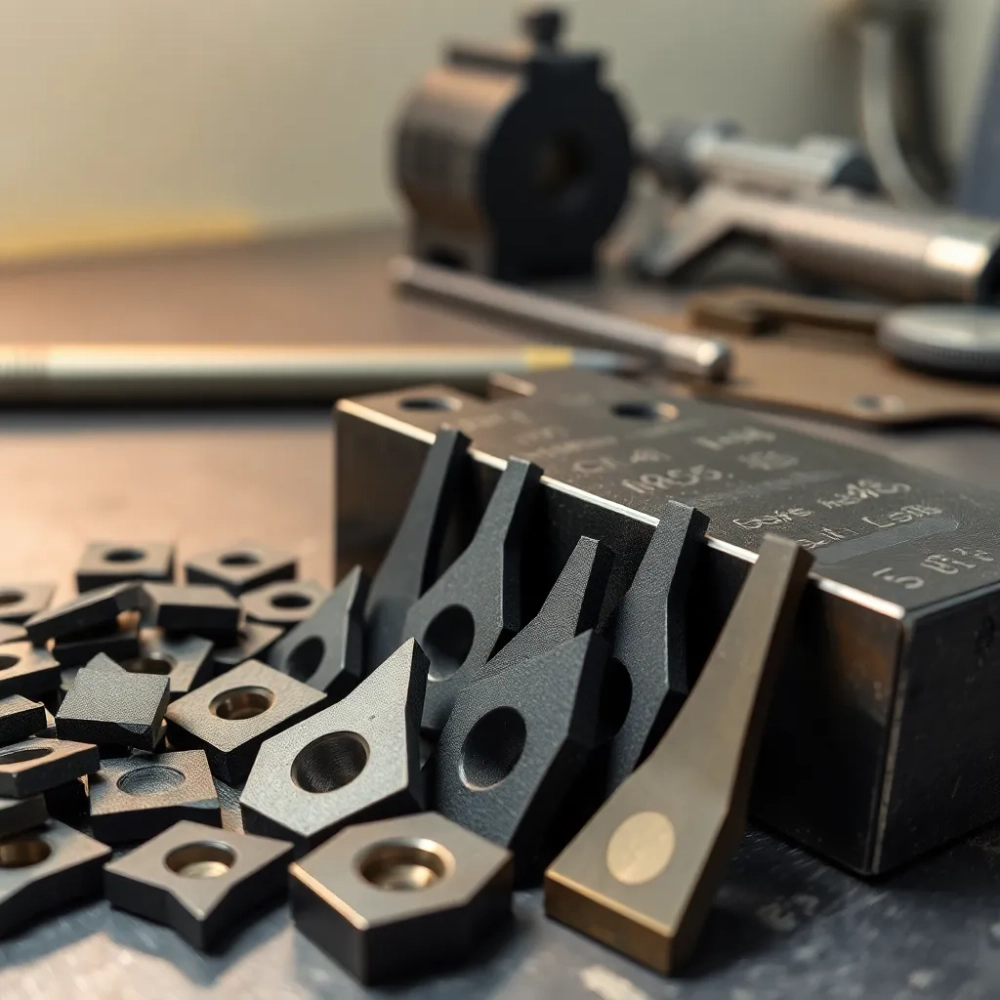
W 2025 roku, bazując na analizie setek przypadków wdrożeń w różnych zakładach produkcyjnych, można zauważyć pewne trendy. Płytki ceramiczne, choć kuszą ceną, często zawodzą przy stali HRC powyżej 60. Z kolei CBN (azotek boru) to "mercedes" wśród płytek, ale i jego cena potrafi "zabrać dech w piersiach". Poniżej zestawienie, które rzuca światło na wybory ekspertów:
Materiał płytki | Zakres twardości stali (HRC) | Zastosowanie | Względny koszt |
---|---|---|---|
Węglik spiekany (pokrywany) | 45-65 | Frezowanie, toczenie ogólne | Średni |
CBN (azotek boru) | 55-70+ | Wykańczanie, precyzyjna obróbka | Wysoki |
Ceramika | 40-55 (ograniczone) | Obróbka zgrubna, sporadycznie wykańczanie | Niski |
PCD (diament polikrystaliczny) | 60+ (specjalistyczne) | Ekstremalnie twarde materiały, specjalne aplikacje | Bardzo wysoki |
Wybór płytek do stali hartowanej: Kluczowe aspekty
Obróbka stali hartowanej, nie da się ukryć, to prawdziwe wyzwanie dla każdego zakładu produkcyjnego. To jak próba ujarzmienia dzikiego konia – wymaga odpowiedniego sprzętu i umiejętności. Kluczową rolę w tym procesie odgrywają płytki skrawające. Nie ma tu miejsca na kompromisy – wybór niewłaściwych płytek może skończyć się katastrofą, przypominającą efekt domina, gdzie jeden zły wybór pociąga za sobą kolejne problemy.
Materiał płytki – fundament sukcesu
Zacznijmy od fundamentów, czyli materiału z jakiego wykonana jest płytka. Na rynku królują trzy główne typy, niczym trzej muszkieterowie gotowi do walki z twardą stalą:
- Ceramika: Płytki ceramiczne, te prawdziwe diamenty wśród płytek, charakteryzują się ekstremalną twardością i odpornością na wysokie temperatury. Idealne do obróbki ciągłej i wykańczającej, gdzie liczy się precyzja niczym u chirurga. Ceny za sztukę w 2025 roku oscylują w granicach 80-250 zł, w zależności od geometrii i producenta. Rozmiary najczęściej spotykane to IC09, IC12, IC16.
- Węglik spiekany z CBN: Drugi muszkieter to węglik spiekany z CBN (azotek boru). Oferuje doskonałą kombinację twardości i udarności. To wybór dla tych, którzy cenią sobie wszechstronność i niezawodność. Cena? Nieco niższa niż ceramika, średnio 60-200 zł za sztukę, ale wciąż mówimy o najwyższej półce. Popularne rozmiary to RNMN0903, SNMN1204, DNMG1506.
- Węglik spiekany powlekany: Trzeci muszkieter, węglik spiekany powlekany, to najbardziej ekonomiczna opcja. Dzięki nowoczesnym powłokom, takim jak TiAlN czy PVD, te płytki potrafią zaskoczyć swoją wydajnością. Ceny zaczynają się już od 20 zł za sztukę, a kończą na około 100 zł. Rozmiary i geometrie są niezwykle zróżnicowane, dopasowane do szerokiego spektrum zastosowań.
Geometria i kąty – sekretna broń
Kolejny aspekt to geometria płytki. To nic innego jak kształt ostrza, który niczym ostrze samurajskiego miecza, musi być idealnie dopasowany do zadania. Geometrie dodatnie, neutralne i ujemne – każda z nich ma swoje unikalne właściwości. Płytki z geometrią dodatnią, niczym baletnica, lekkie i zwinne, idealne do obróbki wykańczającej. Z kolei geometria ujemna, niczym ciężki bokser, mocna i agresywna, sprawdzi się przy obróbce zgrubnej. Kąty przyłożenia i natarcia również mają znaczenie – to jak ustawienie żagli na wietrze, decyduje o efektywności skrawania.
Powłoki ochronne – tarcza przed zużyciem
Nie można zapomnieć o powłokach ochronnych. To one, niczym zbroja rycerza, chronią płytkę przed zużyciem i wysoką temperaturą. Powłoki CVD i PVD to dwie główne technologie. CVD, grubsze i bardziej wytrzymałe, idealne do ciężkich warunków. PVD, cieńsze i gładsze, zapewniają lepszą jakość powierzchni. W 2025 roku dominują powłoki wielowarstwowe, łączące najlepsze cechy obu technologii. Przykładowo, płytki z powłoką TiAlN/TiN/AlCrN oferują wydłużoną żywotność i lepszą odporność na ścieranie.
Chłodziwo – eliksir życia
Chłodziwo to nie tylko dodatek, to wręcz eliksir życia dla płytek skrawających. Odpowiednio dobrane chłodziwo odprowadza ciepło, smaruje strefę skrawania i wypłukuje wióry. Emulsje, oleje, a nawet chłodzenie powietrzem – wybór jest szeroki. W przypadku stali hartowanej, szczególnie polecane są emulsje o wysokim stężeniu lub oleje. Koszty chłodziwa w 2025 roku to średnio 5-20 zł za litr koncentratu, w zależności od rodzaju i producenta. Zużycie chłodziwa na jedną operację obróbczą może wynosić od kilku do kilkudziesięciu litrów.
Praktyczne wskazówki – złote myśli
Na koniec, kilka praktycznych wskazówek, niczym mądrości ludowe przekazywane z pokolenia na pokolenie operatorów CNC:
- Zawsze zaczynaj od mniejszych prędkości skrawania i posuwów, a następnie stopniowo je zwiększaj. To jak rozgrzewka przed maratonem – pozwala uniknąć niespodzianek.
- Regularnie kontroluj stan płytki. Zużyta płytka to strata czasu i pieniędzy. Wymiana płytki na czas to jak wymiana opon w samochodzie – bezpieczeństwo i efektywność przede wszystkim.
- Nie bój się eksperymentować! Różne kombinacje płytek, geometrii i parametrów skrawania mogą dać zaskakująco dobre rezultaty. Pamiętaj, że praktyka czyni mistrza.
Wybór płytek do stali hartowanej to nie jest rocket science, ale wymaga wiedzy i doświadczenia. Mając na uwadze kluczowe aspekty – materiał, geometrię, powłoki i chłodziwo – możesz skutecznie ujarzmić nawet najtwardszą stal. Pamiętaj, że dobrze dobrane płytki to inwestycja, która szybko się zwraca, przynosząc oszczędności czasu i pieniędzy. A w dzisiejszych czasach, czas to przecież pieniądz, prawda?
Materiały płytek do stali hartowanej: Ceramika, CBN i inne
Stal hartowana, twarda sztuka. Nie tylko w przenośni, ale i dosłownie. Obróbka tego materiału to prawdziwe wyzwanie, które spędza sen z powiek niejednemu operatorowi CNC. Kluczem do sukcesu, niczym magiczny artefakt w grze RPG, są odpowiednie płytki do stali hartowanej. Ale jakie właściwie wybrać, gdy rynek kusi nas paletą opcji? To pytanie retoryczne, które zadaje sobie każdy, kto choć raz stanął przed koniecznością zmierzenia się z tym twardym orzechem.
Ceramika – Krucha Elegancja w Obróbce Twardzieli
Ceramika. Słowo to przywodzi na myśl delikatne filiżanki, ale w świecie obróbki skrawaniem to prawdziwy twardziel. Płytki ceramiczne, choć pozornie kruche, potrafią zdziałać cuda przy obróbce stali hartowanej. Mamy tutaj dwa główne typy: ceramikę tlenkową (na bazie tlenku glinu) oraz ceramikę azotową (na bazie azotku krzemu). Ta pierwsza, starsza stażem, dobrze radzi sobie z obróbką ciągłą, gdzie stabilność jest królową. Ceramika azotowa, młodsza i bardziej wyrafinowana, to prawdziwy sprinter – świetnie znosi wyższe prędkości skrawania i obciążenia termiczne, idealna do przerywanego cięcia.
Na rynku w 2025 roku królują płytki ceramiczne najnowszej generacji, wzmocnione wąsami krzemowymi. Ceny? Zależne od producenta i geometrii, ale za paczkę 10 sztuk płytek ceramicznych do stali hartowanej trzeba liczyć się z wydatkiem rzędu 500-1500 PLN. Rozmiary? Standardowo od IC0508 do IC1204, ale dostępne są także niestandardowe wymiary na specjalne zamówienie. Pamiętajmy jednak, że ceramika to dama – wymaga delikatnego obchodzenia się. Nie lubi wibracji i gwałtownych zmian temperatury. Ale jeśli potraktujesz ją z szacunkiem, odwdzięczy się piękną, gładką powierzchnią obrobionego elementu.
CBN – Diamentowy Brat w Walce z Najtwardszymi
CBN, czyli kubiczny azotek boru. Jeśli ceramika to twardziel, to CBN jest Chuckiem Norrisem świata obróbki skrawaniem. To materiał, który ociera się o diamentową perfekcję. Płytki CBN to absolutny top, jeśli chodzi o obróbkę stali hartowanej powyżej 55 HRC. Ceny? Tutaj już wchodzimy w wyższą ligę. Pojedyncza płytka CBN to wydatek od 300 do nawet 1000 PLN, w zależności od gatunku i producenta. Ale za tę cenę otrzymujemy narzędzie, które potrafi skrawać stal hartowaną z prędkością światła, zostawiając idealną powierzchnię i precyzję godną szwajcarskiego zegarka.
W 2025 roku na popularności zyskują płytki PCBN (polikrystaliczny CBN) z warstwami nanostruktur. Zwiększają one żywotność i odporność na ścieranie, co w przypadku tak drogich narzędzi ma kluczowe znaczenie. Rozmiary płytek CBN są zazwyczaj mniejsze niż ceramicznych, najczęściej spotykane to IC0302, IC0402, IC0504. Ilości w opakowaniach również mniejsze – zazwyczaj 5 sztuk, co odzwierciedla ich wyższą cenę i specjalistyczne zastosowanie. Płytki CBN to inwestycja, ale inwestycja, która zwraca się w postaci wydajności, jakości i oszczędności czasu. Jak mawiają starzy wyjadacze: "Co tanie, to drogie". W przypadku obróbki stali hartowanej ta maksyma sprawdza się w stu procentach.
Inne Materiały – Alternatywy i Uzupełnienia
Świat płytek do stali hartowanej nie kończy się na ceramice i CBN. Mamy jeszcze kilka asów w rękawie. Cermetale, czyli spieki ceramiczno-metalowe, to ciekawa alternatywa, plasująca się gdzieś pomiędzy węglikiem spiekanym a ceramiką. Są tańsze od ceramiki i CBN, a jednocześnie oferują lepszą odporność na zużycie niż węglik spiekany przy obróbce stali hartowanej o niższej twardości (do 50 HRC). W 2025 roku obserwujemy renesans cermetali z nowymi powłokami PVD, które znacząco poprawiają ich wydajność.
Nie można zapomnieć o węglikach spiekanych. Choć nie są to typowe płytki do stali hartowanej, to w pewnych zastosowaniach, szczególnie przy obróbce wykańczającej stali o niższej twardości po hartowaniu (do 45 HRC), mogą okazać się wystarczające. Kluczem są tutaj odpowiednie gatunki węglika spiekanego z wielowarstwowymi powłokami, które zapewniają odporność na wysokie temperatury i ścieranie. Ceny płytek z węglika spiekanego są znacznie niższe niż ceramicznych i CBN, co czyni je atrakcyjną opcją dla mniej wymagających zastosowań.
Wybór Płytek – Sztuka Kompromisu
Jakie zatem płytki do stali hartowanej wybrać? Odpowiedź nie jest prosta i zależy od wielu czynników. Twardość stali, rodzaj obróbki (toczenie, frezowanie, wiercenie), wymagana jakość powierzchni, budżet – to wszystko ma znaczenie. Nie ma jednej, uniwersalnej płytki, która sprawdzi się w każdej sytuacji. Wybór to sztuka kompromisu, balansowanie pomiędzy wydajnością, jakością i kosztem.
W 2025 roku, dzięki postępowi technologicznemu, mamy do dyspozycji coraz bardziej zaawansowane materiały i geometrie płytek. Producenci prześcigają się w innowacjach, oferując narzędzia, które pozwalają na obróbkę stali hartowanej z coraz większą precyzją i wydajnością. Pamiętajmy jednak, że nawet najlepsze płytki nie zastąpią wiedzy i doświadczenia operatora. Dobre parametry skrawania, stabilne mocowanie, odpowiednie chłodzenie – to równie ważne elementy układanki, które decydują o sukcesie w walce z twardą stalą. A jak wiadomo, diabeł tkwi w szczegółach, a sukces w obróbce stali hartowanej to suma dobrze dobranych detali.
Geometrie płytek skrawających do stali hartowanej: Jak wpływają na obróbkę?
Obróbka stali hartowanej to prawdziwe wyzwanie, niczym próba ujarzmienia dzikiego rumaka. Materiał ten, zahartowany do ekstremalnych twardości, stawia opór narzędziom skrawającym, generuje wysokie temperatury i bywa kapryśny w zachowaniu. Jednym z kluczowych aspektów, który pozwala nam okiełznać ten materiał, jest geometria płytki skrawającej. Wyobraźmy sobie, że płytka to mały architekt, który musi zaprojektować ścieżkę dla wióra – efektu ubocznego naszej pracy. W 2025 roku, dzięki postępowi w mikro-geometrii, architekci ci stali się jeszcze bardziej precyzyjni. Dziś nie mówimy już tylko o 'łamaczu wióra', ale o złożonych systemach mini-kanałów i wypukłości, które niczym labirynt kierują wiór tam, gdzie chcemy, zapobiegając jego niekontrolowanemu plątaniu się wokół narzędzia i obrabianego przedmiotu.
Wyzwania obróbki stali hartowanej: Pole minowe dla narzędzi
Stal hartowana, niczym forteca, broni się przed każdym ostrzem. Jej wysoka twardość (często powyżej 50 HRC, a nierzadko i 60 HRC) to prawdziwe "być albo nie być" dla narzędzi skrawających. Tradycyjne płytki z węglika spiekanego często kapitulują, poddając się starciu z tym wymagającym przeciwnikiem. Powstaje pytanie: jak w takim razie skutecznie i ekonomicznie obrabiać te "twardziele"? Odpowiedź kryje się między innymi w dobrze dobranej geometrii płytki. To ona decyduje o tym, czy płytka "wgryzie się" w materiał, czy tylko po nim "poślizgnie", generując przy tym niepotrzebne ciepło i drgania.
Geometria płytki: Sekret tkwi w szczegółach
Geometria płytki to nie tylko jej kształt zewnętrzny (kwadrat, trójkąt, romb itd.), ale przede wszystkim precyzyjnie zaprojektowane krawędzie skrawające, kąty przyłożenia, kąty natarcia, promienie naroży, a także – co niezwykle istotne w 2025 roku – mikro-geometria łamaczy wióra. Te pozornie drobne detale mają gigantyczny wpływ na proces skrawania. Zastanówmy się, jak różnią się płytki przeznaczone do stali miękkiej od tych do stali hartowanej. To jak porównanie butów do biegania i butów narciarskich – oba rodzaje obuwia służą do poruszania się, ale w zupełnie innych warunkach i z zupełnie innym przeznaczeniem.
Rodzaje geometrii płytek: Dopasowanie do zadania
W 2025 roku producenci płytek oferują całą paletę geometrii dedykowanych stali hartowanej. Możemy wybierać spośród płytek z ostrymi krawędziami skrawającymi, które niczym skalpel precyzyjnie oddzielają wiór od materiału. Takie geometrie, często oznaczone literą "F" (od finishing), idealnie sprawdzają się przy obróbce wykończeniowej, gdzie liczy się przede wszystkim jakość powierzchni. Z drugiej strony mamy płytki z wzmocnionymi krawędziami, oznaczone np. "M" (od medium) lub "R" (od roughing), które niczym buldożer torują sobie drogę w trudnych warunkach obróbki zgrubnej. Te geometrie, choć mniej ostre, są bardziej odporne na obciążenia udarowe i pozwalają na agresywne posuwy i głębokości skrawania.
- Geometrie "F" (Finishing): Ostre krawędzie, małe promienie naroży, pozytywne kąty natarcia. Idealne do wykańczania, zapewniają doskonałą jakość powierzchni. Cena za 10 sztuk płytek trójkątnych o geometrii F i promieniu naroża 0.2mm w 2025 roku to średnio 250-350 PLN.
- Geometrie "M" (Medium): Uniwersalne, kompromis między ostrością a wytrzymałością. Dobre do obróbki średnio-zgrubnej i wykończeniowej. Cena za 10 sztuk płytek kwadratowych o geometrii M i promieniu naroża 0.4mm w 2025 roku to średnio 300-400 PLN.
- Geometrie "R" (Roughing): Wzmocnione krawędzie, duże promienie naroży, negatywne kąty natarcia. Przeznaczone do obróbki zgrubnej, odporne na duże obciążenia. Cena za 10 sztuk płytek rombowych o geometrii R i promieniu naroża 0.8mm w 2025 roku to średnio 350-450 PLN.
Materiały i powłoki płytek: Zbroja dla narzędzia
Sama geometria to nie wszystko. Równie ważny jest materiał płytki i jej powłoka. W obróbce stali hartowanej królują płytki z węglika spiekanego z powłokami PVD (Physical Vapor Deposition) lub CVD (Chemical Vapor Deposition). Powłoki te, niczym tarcza ochronna, zwiększają odporność na zużycie, temperaturę i utlenianie. W 2025 roku popularne są powłoki wielowarstwowe, które niczym "kanapka" składają się z kilku warstw o różnych właściwościach. Przykładowo, warstwa zewnętrzna może być twarda i odporna na ścieranie, a warstwa wewnętrzna – bardziej elastyczna i odporna na pękanie.
Parametry skrawania a geometria płytek: Taniec narzędzia i materiału
Dobór geometrii płytki to jedno, ale równie istotne jest odpowiednie dobranie parametrów skrawania. Prędkość skrawania, posuw, głębokość skrawania – to wszystko musi być precyzyjnie dostrojone do konkretnej geometrii i rodzaju stali hartowanej. Wyobraźmy sobie, że to taniec – narzędzie i materiał muszą poruszać się w harmonii, aby uzyskać pożądany efekt. Zbyt duża prędkość skrawania przy nieodpowiedniej geometrii może doprowadzić do przegrzania i uszkodzenia płytki. Z kolei zbyt mały posuw przy agresywnej geometrii może generować drgania i pogorszyć jakość powierzchni. W 2025 roku coraz popularniejsze stają się systemy wspomagania CAM, które na podstawie danych o geometrii płytki i rodzaju materiału automatycznie dobierają optymalne parametry skrawania. To niczym automatyczny pilot w samolocie – pozwala uniknąć błędów ludzkich i zwiększyć efektywność procesu.
Praktyczne przykłady doboru geometrii: Z życia wzięte
Powiedzmy, że mamy zadanie obróbki wałka z stali hartowanej 60 HRC. Chcemy wykonać operację toczenia wykończeniowego. Jaką geometrię płytki wybrać? Z doświadczenia wiemy, że w takim przypadku najlepiej sprawdzą się płytki trójkątne z geometrią "F" i małym promieniem naroża (np. 0.2mm). Dzięki ostrym krawędziom i pozytywnemu kątowi natarcia uzyskamy gładką powierzchnię i precyzyjny wymiar. Z kolei, jeśli musimy wykonać obróbkę zgrubną odkuwki z stali hartowanej 55 HRC, lepszym wyborem będą płytki kwadratowe lub rombowe z geometrią "R" i większym promieniem naroża (np. 0.8mm). Te płytki, choć mniej ostre, są bardziej wytrzymałe i pozwolą na agresywne usuwanie materiału. Pamiętajmy, że dobór geometrii to często kwestia prób i błędów, ale znajomość podstawowych zasad i doświadczenie są tutaj kluczowe. Jak mówi stare przysłowie: "Praktyka czyni mistrza".
W 2025 roku, wybór płytek do stali hartowanej to nie tylko kwestia ceny, ale przede wszystkim świadomego dopasowania geometrii do konkretnego zadania i warunków obróbki. Inwestycja w odpowiednią geometrię to inwestycja w efektywność, jakość i trwałość narzędzi. A w dzisiejszych czasach, gdzie liczy się każda sekunda i każdy mikrometr, to inwestycja, która szybko się zwraca.
Parametry skrawania płytek do stali hartowanej: Optymalizacja procesu
Wybór odpowiednich płytek: Fundament obróbki
Zacznijmy od sedna problemu – jakie płytki do stali hartowanej wybrać, by praca nie zamieniła się w koszmar. Wybór odpowiedniej płytki to pierwszy i kluczowy krok. Wyobraźmy sobie, że próbujemy wbić gwóźdź młotkiem do masła. Bez sensu, prawda? Podobnie jest z obróbką stali hartowanej. Potrzebujemy narzędzia, które sprosta wyzwaniu. Na rynku w 2025 roku królują trzy główne typy płytek: ceramiczne, z azotku boru (CBN) i węglikowe z zaawansowanymi powłokami.
Płytki ceramiczne, niczym samurajskie miecze, twarde i kruche, idealnie nadają się do wykańczania powierzchni, gdzie liczy się precyzja, a nie szybkość. Ich cena w 2025 roku waha się od 50 do 150 złotych za sztukę, w zależności od geometrii i producenta. Rozmiary najczęściej spotykane to ISO standardy, czyli np. SNMG120408. Z kolei płytki CBN, prawdziwi twardziele, są bezkonkurencyjne w obróbce najtwardszych stali, tam gdzie inne płytki kapitulują. Cena CBN jest wyższa, od 200 do nawet 500 złotych za sztukę, ale ich wydajność i trwałość często rekompensują wyższy koszt. Dostępne w podobnych rozmiarach co ceramika, ale także w specjalistycznych formatach do konkretnych zastosowań.
Trzecia opcja, płytki węglikowe z powłokami, to wszechstronni gracze. Dzięki nowoczesnym powłokom PVD i CVD, takim jak TiAlN czy AlCrN, potrafią zaskoczyć swoją wydajnością w obróbce stali hartowanej o średniej twardości. Cena płytek węglikowych jest najbardziej zróżnicowana, od 20 złotych za podstawowe modele do 200 złotych za zaawansowane płytki z geometrią i powłokami dedykowanymi stali hartowanej. Rozmiary? Cała gama, od malutkich VCGT090204 po większe CNMG160612, by każdy znalazł coś dla siebie.
Parametry skrawania: Diabeł tkwi w szczegółach
Mając już odpowiednie płytki, czas na ustawienie parametrów skrawania. To jak strojenie instrumentu przed koncertem. Zbyt duża prędkość skrawania (vc) i płytka "spłonie" szybciej niż zdążysz powiedzieć "ups". Zbyt mała prędkość to stracony czas i produktywność. Dla płytek ceramicznych w 2025 roku zalecane prędkości skrawania stali hartowanej (55-65 HRC) to zakres 80-150 m/min. Dla CBN - tutaj możemy poszaleć, nawet do 250-400 m/min. Płytki węglikowe plasują się gdzieś pośrodku, 100-200 m/min, w zależności od powłoki i twardości stali.
Posuw (f) to kolejny kluczowy parametr. Za duży posuw i płytka może się ukruszyć, za mały – drgania i słaba jakość powierzchni gwarantowane. Dla płytek ceramicznych posuw na obrót (fn) to zazwyczaj 0.05-0.15 mm/obr. CBN lubi trochę większe wartości, 0.1-0.25 mm/obr. Węgliki, standardowo 0.08-0.2 mm/obr. Głębokość skrawania (ap)? Tutaj zasada jest prosta – lepiej kilka mniejszych przejść niż jedno głębokie, szczególnie przy stali hartowanej. Dla płytek ceramicznych i węglikowych, 0.1-0.5 mm na przejście to rozsądny zakres. CBN potrafi więcej, nawet do 1 mm, ale ostrożność zawsze popłaca.
Optymalizacja procesu: Sztuka kompromisu i chłodzenia
Optymalizacja parametrów skrawania to ciągłe poszukiwanie złotego środka. Chcemy skrawać szybko, ale nie kosztem trwałości płytki. To jak taniec na linie – trzeba znaleźć balans. W praktyce, często zaczynamy od rekomendowanych parametrów producenta płytek, a potem delikatnie je modyfikujemy, obserwując zachowanie narzędzia i jakość obrobionej powierzchni. Pamiętajmy, że stal hartowana generuje dużo ciepła podczas obróbki. Chłodzenie jest absolutnie niezbędne. Emulsja chłodząca, podawana pod ciśnieniem, to standard w 2025 roku. Można też rozważyć chłodzenie przez narzędzie, co jest szczególnie efektywne przy płytkach CBN.
Drgania? Wróg numer jeden przy obróbce stali hartowanej. Sztywna maszyna, mocne zamocowanie przedmiotu obrabianego i odpowiedni dobór geometrii płytki to podstawa. Czasami pomaga zmiana strategii skrawania, np. z toczenia wzdłużnego na poprzeczne. Pamiętajmy, że obróbka stali hartowanej to maraton, a nie sprint. Cierpliwość, precyzja i doświadczenie to klucz do sukcesu. Aha, i jeszcze jedno – nie zapominajmy o BHP! Stal hartowana to twardy przeciwnik, ale z odpowiednimi płytkami i parametrami, możemy go pokonać.
Praktyczne aspekty i dane z 2025 roku
Podsumowując, wybór płytek do stali hartowanej w 2025 roku to szeroki wachlarz możliwości. Ceny, jak wspomniano, są zróżnicowane, ale inwestycja w dobrej jakości płytki zwraca się w postaci wydajności i jakości obróbki. Dostępność płytek jest bardzo dobra, zarówno w standardowych rozmiarach, jak i specjalistycznych geometriach. Producenci oferują szerokie wsparcie techniczne, w postaci katalogów, aplikacji mobilnych i konsultacji z doradcami.
Przykładowe ceny i ilości płytek w opakowaniach (dane z 2025 roku):
Typ płytki | Model (przykład) | Cena za sztukę (PLN) | Ilość w opakowaniu |
---|---|---|---|
Ceramiczna | SNMG120408 | 80 | 10 |
CBN | CNGA120408 | 350 | 1 |
Węglikowa (powłoka TiAlN) | DNMG150408 | 60 | 10 |
Węglikowa (powłoka AlCrN) | VNMG160404 | 120 | 10 |
Pamiętajmy, że powyższe dane są orientacyjne i mogą się różnić w zależności od producenta, dystrybutora i aktualnych promocji. Zawsze warto porównać oferty i skonsultować wybór z doświadczonym specjalistą. Obróbka stali hartowanej to wyzwanie, ale z odpowiednią wiedzą i narzędziami, staje się fascynującą przygodą.
Chłodzenie i smarowanie przy obróbce stali hartowanej: Kluczowe wskazówki
Obróbka stali hartowanej to prawdziwe wyzwanie, niczym taniec z ogniem. Wymaga precyzji chirurga i cierpliwości zen mistrza. W sercu tego procesu leży wybór odpowiednich narzędzi, a konkretnie – płytek do stali hartowanej. Jednak nawet najlepsze płytki to tylko połowa sukcesu. Druga, równie istotna, to efektywne chłodzenie i smarowanie. Bez tego, całe przedsięwzięcie przypominałoby próbę gaszenia pożaru benzyną - efekt odwrotny od zamierzonego.
Dlaczego chłodzenie i smarowanie jest tak ważne?
Stal hartowana, jak sama nazwa wskazuje, jest twarda i odporna. Podczas obróbki generuje ogromne ilości ciepła. Wyobraź sobie, że próbujesz rzeźbić w lodzie dłutem rozgrzanym do czerwoności – szybko stracisz kontrolę, a efekt będzie daleki od zamierzonego. Podobnie dzieje się przy obróbce stali hartowanej bez odpowiedniego chłodzenia. Temperatura w strefie skrawania gwałtownie rośnie, co prowadzi do:
- Szybszego zużycia płytek skrawających – ich żywotność może skrócić się nawet o 50% w ekstremalnych przypadkach.
- Powstawania naprężeń termicznych w obrabianym materiale – co może skutkować deformacjami i pęknięciami.
- Pogorszenia jakości powierzchni – nierówności, przypalenia, mikrospękania stają się niechcianymi gośćmi.
- Zmniejszenia dokładności wymiarowej – rozszerzalność cieplna materiałów robi swoje.
Smarowanie natomiast, to nic innego jak oliwa w trybach precyzyjnej maszynerii. Zmniejsza tarcie pomiędzy płytką a materiałem, ułatwiając proces skrawania i chroniąc zarówno narzędzie, jak i obrabiany przedmiot.
Jakie chłodziwa i smary wybrać?
Rynek oferuje szeroki wachlarz chłodziw i smarów, niczym paletę barw malarza. Wybór odpowiedniego preparatu zależy od wielu czynników, m.in.:
- Rodzaju stali hartowanej – jej składu chemicznego i twardości.
- Rodzaju obróbki – toczenie, frezowanie, wiercenie.
- Parametrów skrawania – prędkości skrawania, posuwu, głębokości skrawania.
- Typu płytek do obróbki stali hartowanej – materiału, geometrii.
Najczęściej stosowane są:
- Emulsje – mieszaniny oleju mineralnego z wodą. Dobre do uniwersalnych zastosowań, zapewniają dobre chłodzenie i smarowanie. Cena za 20 litrowy kanister dobrej jakości emulsji to około 150-300 PLN.
- Oleje syntetyczne – charakteryzują się lepszymi właściwościami smarnymi i chłodzącymi niż emulsje, szczególnie przy wysokich temperaturach. Są jednak droższe, 20 litrów może kosztować od 300 do 600 PLN.
- Oleje mineralne – stosowane głównie do obróbki z niskimi prędkościami skrawania, gdzie smarowanie jest ważniejsze niż chłodzenie. Cena zbliżona do emulsji.
- Chłodziwa półsyntetyczne – kompromis pomiędzy emulsjami a olejami syntetycznymi, oferują dobre właściwości w średniej cenie.
- Chłodzenie powietrzem lub mgłą olejową (MQL - Minimum Quantity Lubrication) – coraz popularniejsze, szczególnie przy obróbce z wysokimi prędkościami skrawania. Minimalizuje zużycie chłodziwa i jest bardziej ekologiczne. Koszt systemu MQL to inwestycja rzędu kilku tysięcy PLN, ale w dłuższej perspektywie może się zwrócić.
- Zalewanie – najprostsza metoda, chłodziwo po prostu spływa na obrabiany przedmiot. Mało efektywne przy obróbce stali hartowanej.
- Podawanie strumieniem – chłodziwo kierowane jest strumieniem bezpośrednio w strefę skrawania. Bardziej efektywne niż zalewanie, ale nadal może być niewystarczające przy wysokich temperaturach.
- Podawanie przez wrzeciono (CTS - Coolant Through Spindle) – chłodziwo podawane jest przez specjalne kanały w narzędziu, bezpośrednio na krawędź skrawającą. Najefektywniejsza metoda, szczególnie przy wierceniu i frezowaniu głębokich otworów. Wymaga jednak specjalistycznego oprzyrządowania, co wiąże się z dodatkowym kosztem.
- Utrzymuj chłodziwo w czystości – regularnie filtruj i wymieniaj chłodziwo, zanieczyszczone chłodziwo traci swoje właściwości i może powodować korozję.
- Monitoruj temperaturę chłodziwa – przegrzane chłodziwo staje się mniej efektywne. Idealna temperatura to zazwyczaj 20-30°C.
- Stosuj odpowiednie stężenie chłodziwa – zbyt niskie stężenie może być niewystarczające, zbyt wysokie może powodować problemy z pienieniem i osadzaniem się. Zazwyczaj dla emulsji jest to 5-10%.
- Nie bój się eksperymentować – każda obróbka jest inna, czasem trzeba po prostu metodą prób i błędów znaleźć optymalne ustawienia. Pamiętaj jednak o bezpieczeństwie!
Metody podawania chłodziwa
Sposób, w jaki dostarczamy chłodziwo do strefy skrawania, ma niebagatelne znaczenie. Możemy wyróżnić kilka podstawowych metod:
Praktyczne wskazówki i triki
Obróbka stali hartowanej to nie tylko sucha teoria, ale przede wszystkim praktyka. Oto kilka wskazówek, które mogą okazać się bezcenne w warsztacie:
Chłodzenie i smarowanie to nie dodatek, ale integralna część procesu obróbki stali hartowanej. Odpowiedni dobór płytek i wspomagających je płynów chłodząco-smarujących to klucz do sukcesu, czyli wydajnej, precyzyjnej i ekonomicznej obróbki. Pamiętaj, że oszczędność na chłodziwie to jak oszczędność na hamulcach w samochodzie – może się skończyć tragicznie. Inwestycja w dobre chłodzenie i smarowanie to inwestycja w jakość i trwałość – zarówno narzędzi, jak i wykonanych detali.